Custom Dashboards
The Benefits
- Near Real Time Dashboards
- Monitor ANY Aspect of Your Business
- Interactive
- Simple
- Custom to Your Business
- Access From Any Device
- Integrate with Current Software
Sample Questions That Our Dashboards Answer
- Who is your TRUE customer?
- How many people are visiting your website and when?
- Are sales increasing even accounting for seasonality?
- Did ALL aspects of your business do better this period compared to last period?
- How is the quality of my product from the perspective of my customer? How about my employees perspective?
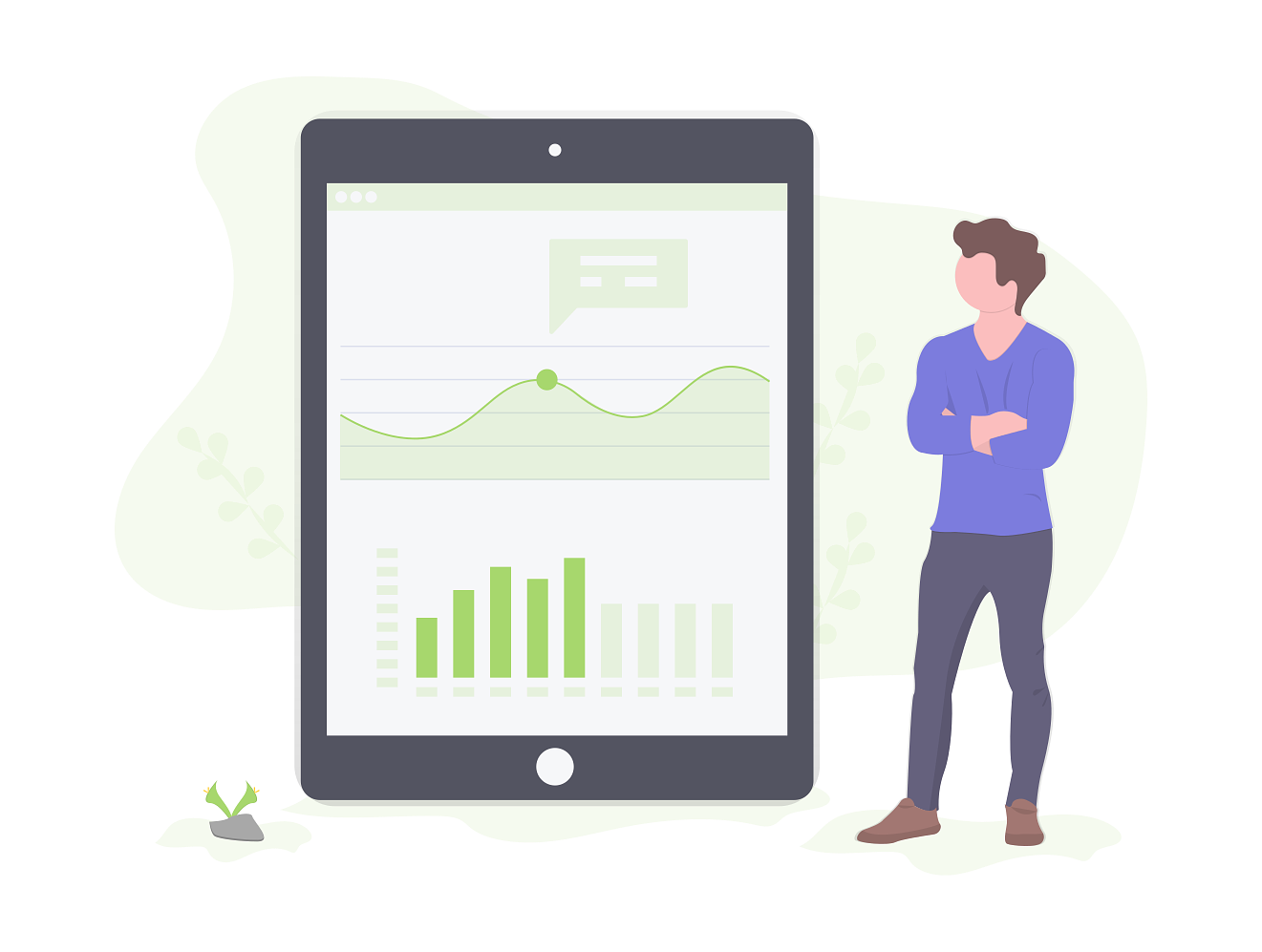
Project Services
At Cholla Automation, we don’t just help you identify problems and opportunities for improvement with our dashboards. We also help solve problems that are plaguing your business and help improve current business processes.
Our project team consists of highly experienced LEAN SIX SIGMA and risk management experts to help your continuous and quality improvement efforts. These methodologies have been proven to work in any industry with great documented success.
Whatever your problem may be, we can solve it!